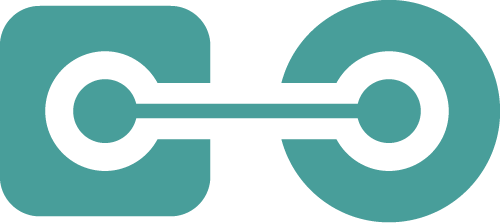
TEFS
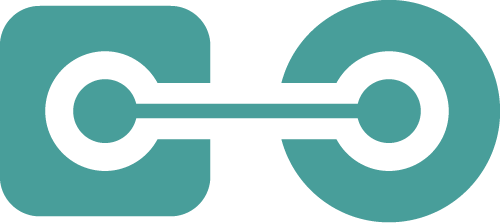
Testing and Expimentation Facilities
Four testing facilities all over Europe offer the expertise and infrastructure for your HRI
Experimental Robotic cell for Complex Picking and Dismantling Applications [CARTIF]

Innovation is at the forefront of our TEF1, providing unparalleled support in experimental design and human-robot interaction research innovation. It is a hub for designing and conducting experiments related to human-robot interaction, evaluating robot behaviour adaptation algorithms, testing, or assessing the impact of collaborative tasks on productivity.
This TEF is for manufacturers, assembly lines, and logistics operators utilising our facilities to test and refine robotic systems designed to streamline production processes. Here, you can develop new algorithms and control strategies that make robots more intuitive, adaptable, and collaborative. This not only boosts efficiency but also enhances workplace safety, making TEF1 a critical supportive player in the future of your industrial operations.
We are pushing the boundaries of human-robot interaction
In TEF1 we offer a diverse range of experimental opportunities aimed at advancing human-robot interaction (HRI) in industrial settings. Some of our key projects include:- Adapting Robot Behavior to Operator Conditions: We focus on creating algorithms that allow robots to modify their behavior based on the operator’s condition and preferences, making interactions more seamless and efficient.
- Identification of Complex Objects: Together we develop sophisticated computer vision and machine learning techniques that enable robots to identify and handle complex objects within their environments.
- Human-Robot Interfaces Using XR (Extended Reality): By leveraging XR technologies, we create intuitive and immersive interfaces that allow users to interact with robots naturally. These interfaces overlay digital information onto the physical world, enhancing the user experience.
- Human-Robot Interfaces Using Natural Language: We develop natural language tools that enable humans to interact with robots through spoken commands. This allows robots to understand and respond to verbal instructions in real-time, making interactions more fluid and human-like.
We are addressing real-world challenges of our industries.
In ARISE a particular focus is on:
- Dismantling and Assembly of High-Value Products: Developing precise and reliable methods for handling items.
- Complex Picking in Warehouse Environments: Enhancing robots’ ability to navigate and perform tasks in dynamic warehouse settings.
Driving Innovation and Collaboration
Our overarching goal in TEF1 is to enhance HRI and collaboration in industrial settings, driving improvements in productivity, efficiency, and safety across various industries. By fostering collaborative research and development, we aim to seamlessly integrate robotic systems into existing workflows, augmenting human capabilities and driving transformative changes in industrial production and logistics. Ultimately, TEF1 serves as a catalyst for innovation, empowering users to unlock the full potential of collaborative robotics in industrial environments.
Re-programmable Co-bots for Flexible Manufacturing [INT]
Pioneering Robotics and Industry Collaboration in Italy
TEF2 is also known as JOiiNT LAB, was established in 2020 as a partnership between Istituto Italiano di Tecnologia (IIT) and Intellimech.
This state-of-the-art laboratory is dedicated to advanced robotics technologies, with a mission to bridge the gap between cutting-edge research and industrial applications. By fostering high-level professional training and promoting technological excellence, JOiiNT LAB joint laboratory is unique in terms of size and strategic importance, making it stand out as a beacon of innovation within the local and national industry landscape.
A centre of synergy and innovation
JOiiNT LAB is unique, serving as the perfect platform for IIT’s efforts to support regional and national industries. The lab is a node where institutions, research organizations, academic entities, and industrial companies meet. The mix of researchers and engineers from industrial partners creates a fertile environment for the exchange of ideas and expertise, driving forward technological advancements and meeting industrial needs with precision.
Collaborative Efforts for impactful practice-based solutions
Building on its advanced technologies and expert competencies, JOiiNT LAB has identified four key use cases to address industrial challenges:
- Flexible Robotic Workstation: Enhancing versatility and efficiency in manufacturing processes.
- A Robotic Assistant: Providing support and improving productivity in various tasks.
- Logistic 4.0: Revolutionizing logistics with smart, automated solutions.
- Robot Avatar for Remote Physical Activities: Enabling remote operations and interactions through advanced robotics.
These 4 use cases represent different aspects and challenges commonly faced by industries requiring humans and robots to collaborate and work effectively together to be successful.
By bringing together the best minds from research and industry, JOiiNT LAB creates an environment where technological innovations are developed and seamlessly integrated into real-world applications. This supports the evolving needs of industries and ensures that technological advancements are both practical and impactful.
Revolutionizing Healthcare with Human-Centered Robotics [PAL]
Located at PAL Robotics TEF 3 is dedicated to testing and refining robotic technology, especially tailored for healthcare environments. This specialized hub offers adaptable settings that simulate various real-life scenarios, providing a rich ground for innovation and development. Here, PAL Robotics leverages advanced platforms like TIAGo Pro’s digital twin to push the boundaries of what’s possible in healthcare robotics.
A human-centred approach to Robotics in Healthcare
At TEF 3, the focus is on a human-centered design to ensure that robotic systems seamlessly enhance healthcare delivery. The primary mission is to develop a robust Human-Robot Interaction (HRI) framework that enables robots to exhibit clear, understandable behaviors. One of the key applications of this technology is in fetch and carry tasks within healthcare settings. Robots are designed to assist by transporting specific items to designated locations, allowing healthcare staff to devote more time to patient care rather than routine transport tasks.
Transforming Routine Tasks going beyond traditional robotics
In TEF3 robots are tested for their ability to assist with everyday tasks. Using multimodal social signals such as voice commands, gestures, and gaze, these robots interact intuitively with hospital staff, making the technology user-friendly and efficient. This initiative aims to transform robots from mere mechanical assistants into intuitive, empathetic partners in patient care.
But this is not just about enhancing task-based functionalities. The second focus of TEF3 is to develop an advanced HRI layer that transcends traditional robotic capabilities. This involves creating systems that understand and adapt to human conditions, preferences, and environmental interactions. By doing so, PAL Robotics is paving the way for a new generation of healthcare robots that are not only functional but also adaptive and responsive to the needs of their human counterparts.
Leading the way towards human-centric zero-defect manufacturing [POLIMI]
Part of the university Politecnico di Milano, TEF4 is also known as the Industry 4.0 lab, a laboratory fully equipped with industrial assets in order to create a realistic environment for testing research findings and developing customised solutions based on cutting-edge equipment and technological solutions.
Leveraging the modular and flexible facilities, POLIMI transforms its Industry 4.0 Lab into a testbed for innovative experiments and technological advancements. As part of a public university, this lab also serves as a didactic factory, providing students with hands-on training in real-world conditions.
A fertile ground for the solutions of tomorrow.
Within the ARISE project, POLIMI Industry 4.0 Lab acts as a Testing and Experimentation Facility (TEF) addressing “Human centric zero-defect manufacturing” framework.
Here, two main challenges are explored through relevant application cases, allowing stakeholders to witness firsthand how these technical hurdles are addressed in a realistic testbed environment:
- Challenge One: Enhancing Worker Efficiency in High-Precision Tasks
The first challenge at POLIMI’s TEF is centered around using HRI for improving the efficiency of workers engaged in high-precision, flexible tasks within manufacturing settings. Typically, technicians tasked with manual reworking of defective intermediate goods must navigate a diverse array of processes and tools. This often leads to time-consuming setup and selection activities that detract from value-adding work. POLIMI’s innovative solution leverages production line data to predict and arrange the necessary tools and workspace for each technician, optimizing efficiency and accommodating individual preferences. This approach not only streamlines operations but also empowers workers to focus on their core tasks with greater precision and effectiveness.

- Challenge Two: Improving Ergonomics in High-Precision Tasks
The second challenge addresses the HRI supported improvement of ergonomics in high-precision tasks. POLIMI’s system envisions a collaborative robot capable of picking up goods to be reworked from their carrier and placing them in a fixed location tailored to the technician’s physical characteristics, such as height. This human-robot interaction solution aims to enhance ergonomics, ensuring that technicians can perform their tasks comfortably and efficiently. By prioritizing the physical well-being of operators, POLIMI’s approach not only improves productivity but also fosters a healthier, more sustainable work environment.
